Selection Of Honing Oil
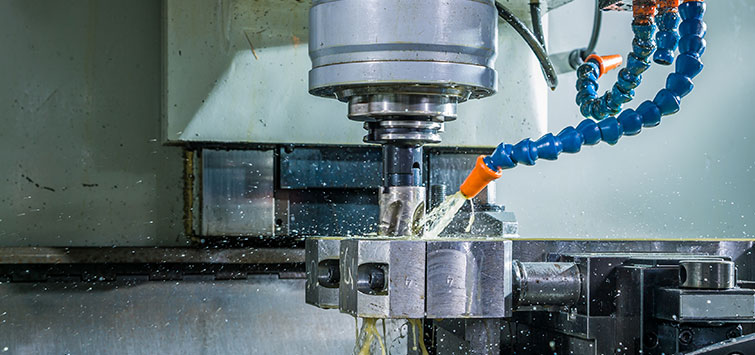
Honing is an abrasive process (similar to grinding) at comparatively slow speed from which the stock is removed from metallic or non-metallic surfaces by a bonded abrasive sticks called honing sticks/tools.
Honing oils improve the accuracy and finish of automobile cylinder bores, hydraulic cylinders, and similar parts. The honing machine consists of four fine-grain abrasive stones attached to an expandable tool that is then slowly revolved and oscillated inside the cylinder until the desired finish and diameter are obtained. In honing oils process simultaneous rotating and reciprocation motion is given to the stick and the surface thus produced will have a characteristic cross-hatch lay (Honeycomb type) pattern
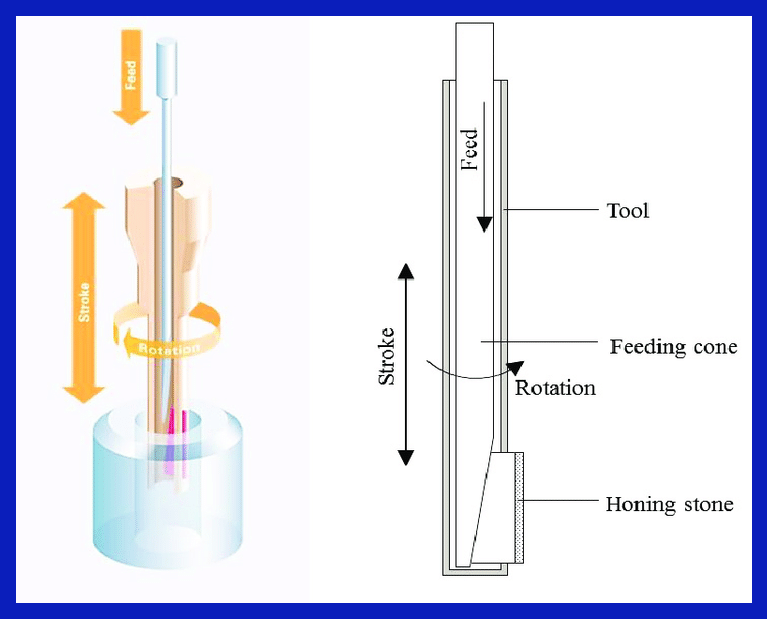
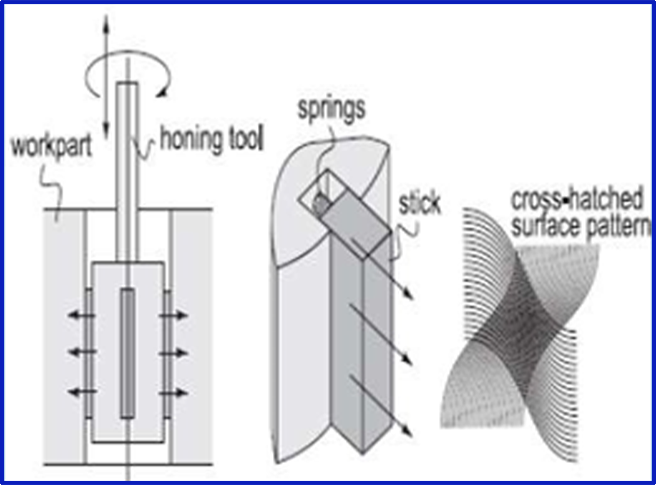
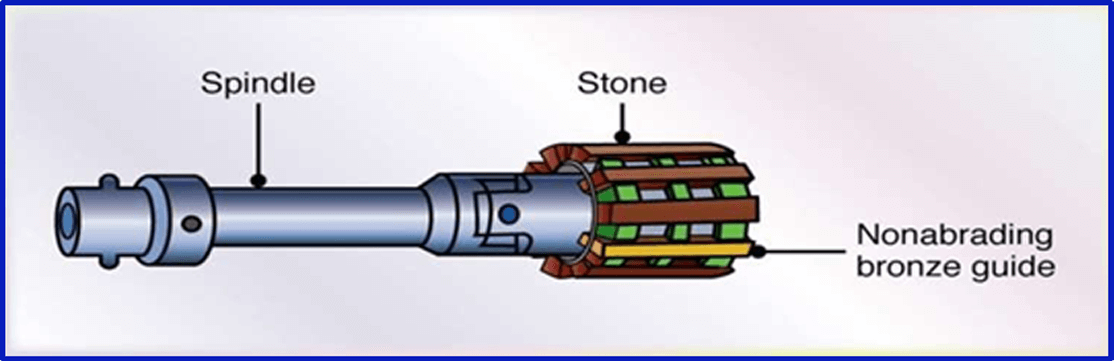
Comman Industries
- Automotive
- Aerospace
- Oil & Gass
- Industrial equipment's (cylinder barrels, etc.)
General Parts for Honing Application
- Bearing rings
- Cylinder blocks
- Connecting rods
- Crank Shaft
- Cam shafts
- Wheel cylinders
- Hydraulic parts (Pistons, rods, rings, etc.)
- Valves
- Fuel injectors
- Gears
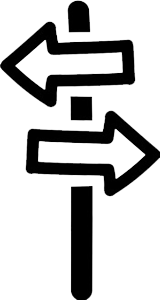
Different Types Of Finishing Applications
Honing is a finishing process used to improve the geometry of a part, readjust the alignment of features such as holes or bores, and produce a finer surface finish. In the honing process, a small, bonded, abrasive stone or super-abrasive stick is rotated over the surface of a part over a controlled path.
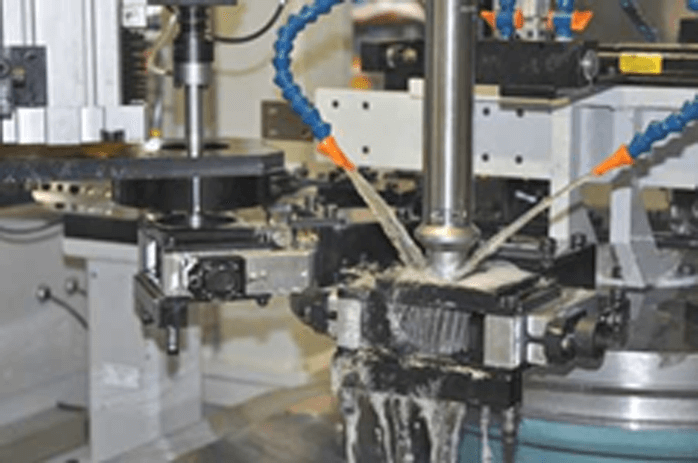
Vertical Honing
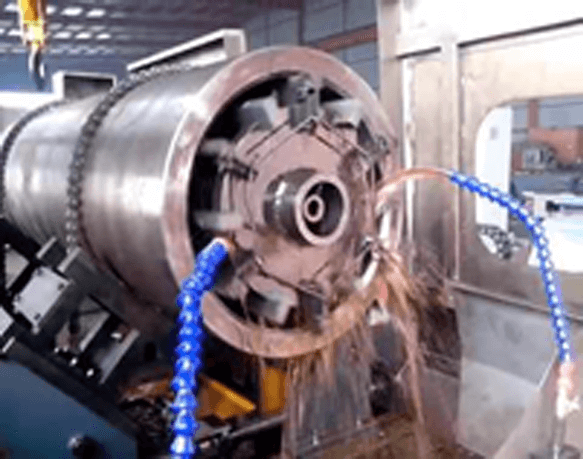
Horizontal Honing
Superfinishing is used to refine the surface finish of a component to produce a very fine surface with an exceptionally low roughness average (RA). A fine-grit abrasive stone or tape is rotated over the component while the component is simultaneously spun in the opposite direction. This process removes the amorphous surface layer left by the last grinding process and leaves a recognizable crosshatch pattern. Superfinishing will increase the life of a part by decreasing wear and tear.
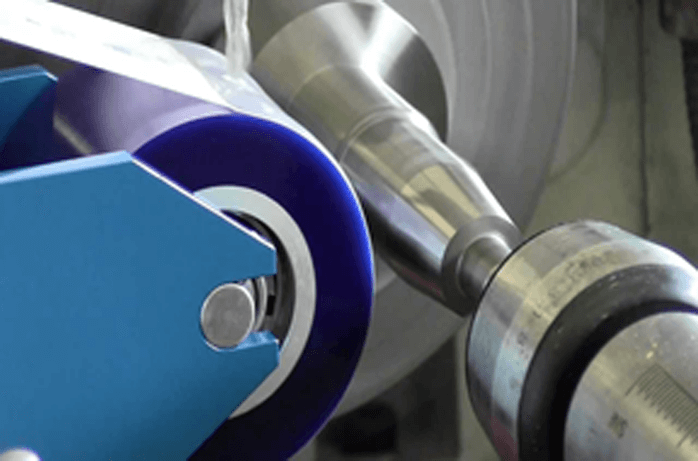
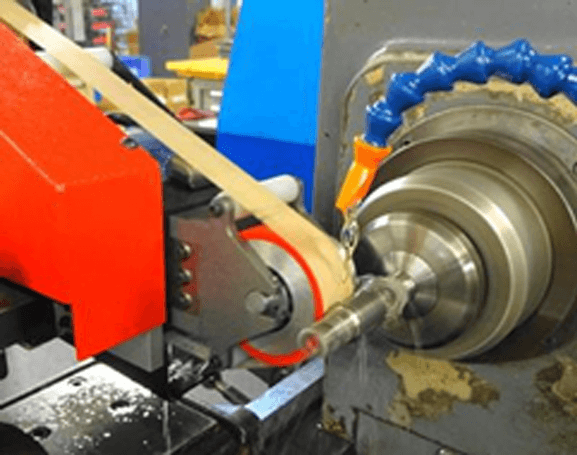
Honing Super finishing Oil
The high-performance specification of honing oils and finishing oils are formulated with a select blend of base fluids and additives that are safe for use with all types of materials.
The low-viscosity honing oil is blended with or without chlorine and sulfur additives, antioxidants, extreme-pressure additives, and synthetic ester lubricity additives for honing different metals. The high lubricity of honing oil ensures longer tool life, higher work speeds, and better finish quality. It also helps to achieve good finishes in short-stroke, micro-finishing operations on tough materials like bearing steel and other steels.
Majbrs Factors fluencing Honing application
- Honing/ super finishing fluid
- Honing Tool (Material - Carbides, Blades, Sulphurized key stone, Diamond stones, etc.)
- Honing time
- Honing Length
- Honing pressure
- RPM
- Material
- Filtration
Key requirements of Honing Oil
- Low Viscosity
- EP Additives
- Compatibility with tools and part material
- Good Filterability
- Good sludge/ fines settling proper ies
- Good oxidation St ability
Types of Tools
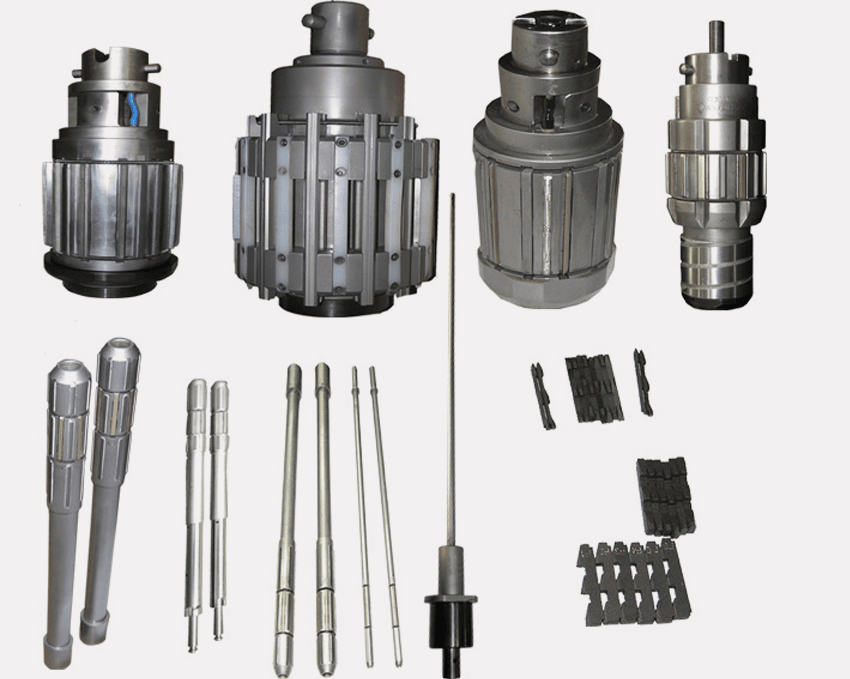
S.No | Features | Advantages |
---|---|---|
1. | Polar and Extreme Pressure additives |
|
2. | Highly refined Base stocks |
|
3. | Low viscosity |
|
4. | Low Copper Strip Corrosion |
|
Different Type of Honing & Super Finishing Oils From Hardcastle
Hardcastle Petrofer is a leading honing oil manufacturer in India. We at Hardcastle Petrofer have developed various types of Honing oils considering the critical operating conditions, operators handling, safety, and health issues.
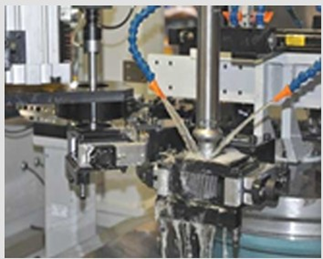
Neat oils
Hicut Hone Series
-With & Without Chlorine
-With & Without Sulphur
lsocut Series
-With modern additive and base oil
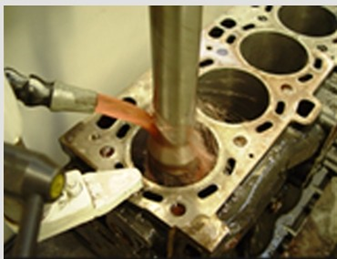
Water Based
Emulcut series - Translucent Micro emulsions
In order to determine the most suitable honing oil for an application, consult our technical experts for their advice in selecting the right product.